-
ATX computer power supply current limit.
(This post is also available in Dutch) For another project I’m tinkering with an old computer power supply. While I’m at it, why not see if I can build some crude current limiting. It does not need to regulate the current neatly, as long as it is short circuit proof. A LED on the 12V…
-
ATX voeding stroombegrenzing.
Ik ben voor een ander project wat aan het prutsen met een oude computervoeding. Nu ik toch aan het prutsen ben, eens kijken of er een simpele stroombegrenzing te klussen valt. Het hoeft geen nette stroomregeling te zijn, als het maar kortsluitvast is. Een LED op een uitgang van een computervoeding zal normaal gesproken onmiddellijk…
-
Some short notes on the Lecroy9450 repair project
Because there is no big news yet, some short updates. – Claude Schwarz pointed me to the Yahoo user group “Lecroy Owners group”, they have design files for a HHZ406 replacement. (Made by Dieter Frieauff). So maybe the ext. trigger input can be repaired as well. – A service manual for this ‘scope (And others)…
-
LeCroy 9450 oscilloscope repair
This was supposed to be an easy repair, and therefore not worth blogging about. But as it turns out, it might get interesting after all. (The ‘scope is not repaired yet) The “Leidse Makerspace” owns a LeCroy 9450 350Mhz DSO. When they moved to their new location I temporarily got this oscilloscope. Not just for…
-
Quick and dirty Arduino optical mouse sensor experiment (a2620 chip)
I wanted to experiment with a optical mouse sensor, did a websearch, found this blogpost, and adapted the code for my A2620 mouse sensor. As it might be useful to others, below is my Arduino sketch and the processing sketch. Use the processing sketch to view the image from the sensor, or use a terminal…
-
3d printed pcb houder
Helaas is het printje net iets groter dan de houder, dus dat wordt het ontwerp wat aanpassen, maar dit is mijn eerste 3d ontwerp en daarvoor vind ik het resultaat best aardig 🙂 Geprint op de Leidse Makerspace: www.makerspaceleiden.nl
-
ESR LC meter behuizing
Ik ben momenteel bezig aan een ESR / L / C meter. In “Boem een blog” was al een foto te zien van het VFD, en een kort verhaaltje over hoe ik dat aanstuur. Hierbij wat foto’s van de bouw van de behuizing. (Het oorspronkelijke plan was om gedurende de bouw te posten wat de…
-
Hotglue reflow
Dit is hoe ik m’n iPAQ (h2200, h2210) z’n batterijklepje heb gerepareerd, met smeltlijm. Om de een of andere reden plakt hotglue beter met een dun laagje tussen de te verbinden delen, ipv een dikke laag. Door met m’n heteluchtsoldeerstation de hotglue (en de te verbinden delen) warm te maken kon ik er zo’n dun…
-
433Mhz spraak transmissie experiment met 1-bit ADC
Toen ik dit las vroeg ik me af of met zo’n 1-bit ADC verstaanbare spraak te verzenden zou zijn met zo’n goedkope 433Mhz module. En dan liefst met een heel simpele quick and dirty 1-bit ADC gemaakt uit standaard onderdelen. En dat blijkt te kunnen! M’n adc is geen echte adc, er is geen kloksignaal…
-
Fixing a broken SD card slot.
Repair companies are completely right they don’t repair on this level of detail, but swap an entire board instead. Much easy-er. But I don’t have spare boards lying around and I like a challenge, so… A friend of mine had a defective digital camera, someone forced the sd card in the wrong way, with bent…
-
Boem! een blog.
Omdat ik m’n website zowat nooit bijwerk heb ik nu ook een blog, om dat eventueel wat vaker bij te werken. Niet gezegd dat ik dat ook doe natuurlijk… Ik ben van plan hier wat elektronicadingetjes te schrijven voor degenen die daarin geïnteresseerd zijn. Lopende projectjes, losse flarden, etc. in een wat losser verband dan…
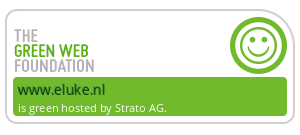